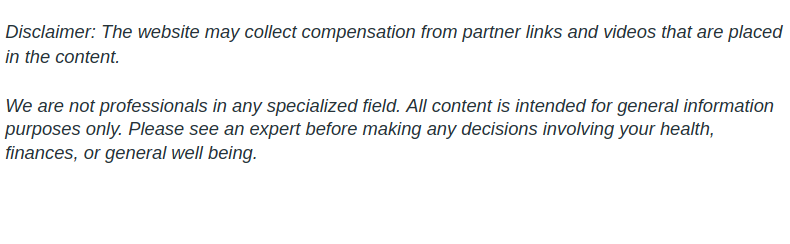

Form fill seal is an assembly line way of product packaging. There are two types of these machines, one being the vertical form fill seal, and the other the horizontal form fill seal. Form fill seal is basically a way of packaging by forming, filling, and sealing the product all on one machine. It creates packaging that is heat sealable, flexible, and can be filled with any kind of product. This type of packaging is typically done with plastic, by loading a flat roll of plastic film into the form fill seal machine. However, other materials can also be used by changing the seaming and sealing methods within the process. Other materials that can be used for packaging are paper, fabric, film and foil.
Vacuum pouches are created by form fill seal machines. They provide a way of packaging by removing all air from the bag before it is sealed. The idea of vacuum pouches is to enable the product to have a longer shelf life. By removing the oxygen from the pouch or bag and sealing it afterwards, bacteria has less chance of growing within the package, therefore increasing safe storage time. In addition, dry goods can be stored for longer periods of time by this process; for instance, nuts, beans, cereal, and coffee. Vacuum packaging foods protects the product between three and five times longer than would the typical container or plastic bag. Studies show that 52% of people in the world make purchasing decisions based on the packaging that the product is in when it is sold. People like to see an effort on the part of the manufacturer toward protecting the environment.
Food shrink bags are a safe and widely used method of packaging. They are used for packaging foods as well as many other products. Food grade vacuum pouches are used for sealing around meats, removing the air from the package and keeping the meat fresh for longer periods of time. In addition, shrink sealing can be used for large household items like pillows and comforters that need to be stored. By using a vacuum, consumers can even use this process at home. By vacuuming the air out of the bag through a special opening, the bag is shrunk tight around the item, reducing its size for safe storage even in the smallest space.
A food metal detector is an essential piece of equipment in the food packaging industry. It is in the assembly line both before and after the machines that perform the actual packaging, so the food is inspected in its raw state as well as after it is packaged and sealed. Unfortunately, although inspections are carefully done of all foods that are ultimately sold to the public, every so often there is something that is missed. Even a microscopic piece of metal within a cut of meat, if gone unnoticed, could cause irrevocable harm to the consumer. This is the first line of consideration and concern. The repercussions to the company itself could also be permanently irreversible. For both these reasons, and everything they bring with them, thorough and careful inspection is imperative by a food metal detector or even an x-ray machine. In spite of the care taken by food inspection, however, every year 48 million people get sick from a contaminant in a food they ate. In addition, 128,000 will be admitted to hospitals for this reason, and 3,000 will lose their lives.
X ray food inspection is, as mentioned briefly, also a way of examining foods for harmful contaminants. It is a way of using electromagnetic energy to see the inside of foods that the naked eye cannot see. Just as x rays are used in the medical field, the same process can be used to see the inside of a cut of meat, no matter how dense it may be. The x ray enters the food, and, as it leaves, a sensor inside the equipment will pick up anything in the food that does not look right. The technician is then able to focus on that spot and make an identification. X ray inspection works well because it can enter a product without causing any impairment to it.